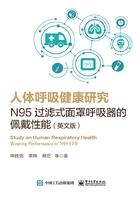
3.2 Models of flow field and particle movement
3.2.1 Flow field and particle movement
The CFD software ANSYS Fluent is widely used to calculate the flow filed,and the DPM embed in ANSYS Fluent is usually used to calculate the particle movement [49-54].However,the DPM treats the particle as a mass point,which does not consider the particle interception by the solid surface and particle deposition.The rebound module in DPM,which supposes that all contacts are elastic collision,cannot simulate the real collision process.Because it must have energy loss by collisions according to different collision conditions and material parameters.Besides,DPM fails to accurately predict particle trajectories when the Brownian motion is not negligible.So,a numerical simulator is developed to solve the above difficulties.The flowchart of our simulations is shown in Fig.3-1.
In this chapter,the fiber applied in the simulation has a diameter of 20μm.Firstly,the air flow field around a row of fibers is simulated by the CFD method.The air flow field in the filtration domain is simulated under the velocity inlet and pressure outlet boundary conditions.A periodic boundary condition is applied to the lateral sides of the simulation domain.Then,the simulation domain is meshed using uniformly distributed triangular elements.In the finite element model,100 grid points on border of the fiber are used to ensure that the simulation results are mesh-independent [49].The air flow through the fibrous media is typically considered to be a steady-state laminar flow [52-53],which has also been validated in the previous study of Hosseini and Tafreshi [49].The finite volume method of Patankar [55] implemented in ANSYS Fluent is used to solve the air flow field deriving from the Navier-Stokes (N-S) equations.The continuity equation and the conservation of momentum equation can be written as follows [51].

Fig.3-1 Flowchart of the simulation


whereρand µ are the density and dynamic viscosity of air;V and p are the velocity vector and pressure of air flow,respectively;t is time,∇is the del operator,and∇2 is the Laplace operator.The Euler-Lagrange (E-L) approach is appropriate for the simulation of the particle movements [53].The particles size is 0.1μm-2.4μm,and the mutual influences of the dynamic particle transport and deposition on the flow field are not considered [49-50,52-53].The self-developed solver employs a fourth order Runge-Kutta method to solve the control equation of particle movement,which is derived from the Newton's Second Law.It also uses the binary Lagrange interpolation method to obtain the air flow velocity located at the current position of target particleU) [56].The equation of motion for a spherical particle in the air flow can be written as

where U is the velocity vector of the flow filed, Upis the velocity vector of the particle,Cc=1+Knp(1.257+is the Cunningham correction factor,where Knp=2λ/dp is the particle Knudsen number, dpis the particle diameter,ρpis the density of the particle,ρis the density of the flow field, Giis a random number chosen from a normal distribution with a zero mean and a unite variance, S0 is the corresponding spectral intensity of the noise given by [36]:S0=
,and g is the acceleration of gravity.
Fig.3-2 shows the percentage of each force as a function of the particle diameter.As shown in Eq.(3-3),the random number Giin the expression of the Brownian force is selected to be unity.And,the velocity disparity (U-Up) between the particle and air flow is 0.2 m/s.The soft Polystyrene Latex (PSL) particle with a density of 1050 kg/m3 [43] is chosen to be analyzed here.It can be seen that the Brownian force is significant for small particles,and its percentage decreases as the particle diameter increases.The percentage of the gravity is 1.5%even for relatively large particle (10 μm),and it increases rapidly as the particle diameter further increases.The percentage of the drag force keeps increasing until the particle diameter increases to 10μm.Then,it decreases dramatically since the gravity gradually becomes dominant.In conclusion,effects of the Brownian force should be considered for submicron-sized particles,and effects of the gravity should be taken into account for micron-sized particles larger than 10μm.

Fig.3-2 The percentage of each force acting on moving particles as a function of particle diameter
3.2.2 Particle rebound model
The schematic of the particle impact and rebound on a fiber surface is shown in Fig.3-3.The collision between a particle and fiber surface can be characterized in terms of the energy of the particle-surface system [41].The particle's normal critical velocity Vin*can be expressed as

where E is the adhesion energy (depth of the attractive potential well), e is the coefficient of restitution,and m is the particle mass.When the normal incident velocity (Vin) is smaller than Vin*,the particle will be captured by the fiber surface [41,44].

where H is the Hamaker constant which varies with the material parameters, z0 is the equilibrium separation of the spheres,and dsis the diameter of the fiber or deposited particle.

Fig.3-3 Schematic of the particle impact and rebound on a fiber surface
If particles contact with and rebound from the solid surface,the velocity ratio of the normal rebound velocity Vrn to Vin can be written as

Dahneke conducted numerous experiments regarding the rebound of soft PSL particles and found that the adhesion energy was substantially larger than that predicted by the classical theory [43,58].This discrepancy was due to the elastic flattening of soft PSL particles.Wang and John also observed that soft particles were more likely to adhere to a fiber surface [59].The soft PSL particles are chosen to be analyzed,and the fiber material is chosen as the polished quartz [43].The adhesion energy for soft PSL particles and coefficients of restitution for collisions can be obtained from Dahneke's results [58].Whether a particle is adhered to or rebounded from a fiber surface will be determined by the particle's normal incident velocity in Eq.(3-4).For particle-fiber collisions and particle-particle collisions,it assumes that:(1) surfaces of particles and fiber are perfectly smooth;(2) particles are nonrotating spheres;and (3) particles stay static after adhesion.
Fig.3-4 shows the calculated Vin*as a function of the particle diameter.The coefficients of restitution (e) for particle-fiber collisions and particle-particle collisions are 0.96 and 0.90,respectively [58].The Vin*for particle-particle collisions is larger than that for particle-fiber collisions at a given diameter,mainly because the coefficient of restitution (e) for particle-particle collisions is smaller than that for particle-fiber collisions (Eq.(3-4)).The Vin*decreases as the particle diameter increases,so larger particles are more likely to rebound from the solid surface and escape away.Particles with a Vin smaller than Vin*will not have enough energy to overcome the potential well of the solid surface,but particles with a Vin larger than Vin*will have enough energy to rebound from the solid surface of the fiber or existing deposited particle.

Fig.3-4 The normal critical velocity as a function of particle diameter
Fig.3-5 shows the velocity ratio (Vrn/Vin) in Eq.(3-6) versus Vin for the particle-fiber collisions and particle-particle collisions with two particle diameters (dp=1μm and 2 μm).The velocity ratios for particle-fiber collisions and particle-particle collisions increase with the increase of Vin,and finally reach an approximate constant value of 0.96 and 0.90,respectively.Therefore,the velocity ratio is close to the coefficient of restitution (e) at a large incident velocity (Vin).Such a conclusion can also be derived from Eq.(3-6) by inputting a large value of Vin.We also observe that the velocity ratio for particle-particle collisions is smaller than that for particle-fiber collisions at a given Vin.Because the coefficient of restitution of particle-particle collisions is smaller,more energy loss occurs due to a larger plastic deformation.

Fig.3-5 Velocity ratio (Vrn/Vin) of particles as a function of Vin