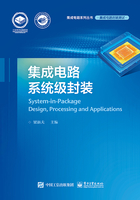
1.1.1 系统级封装技术发展历史
IC制造工艺的发展通常遵循摩尔定律。自三极管发明以来,微电子产业就一直致力于追逐摩尔定律,并追求晶体管的高集成度、低成本。受市场需求与市场竞争的推动及微电子技术的发展,系统级芯片由此产生并得到发展。微电子加工技术目前已跨入超亚微米乃至纳米时代,在单片上可以集成数百万甚至上亿个元器件,从而实现一个完整电子系统。20世纪60年代,有人提出了单一硅基上系统芯片(System-on-Chip,SoC),又称系统级芯片。SoC功能集成示意图如图1-1所示。芯片本身是一个具备特定目标的产品。SoC集成各项功能形成一个完整的系统,同时嵌有基本软件模块或可载入的用户软件,对这个系统进行封装,以提供必要的保护、外部连接、电源,使其发挥计算、通信与其他重要功能(如处理器、存储、无线和图表)。延续摩尔定律的理想发展路线,SoC必将是性能最高、功耗最小、体积最小、质量最轻的单芯片集成系统。SoC技术取得了很大的进步,从IC级到微米级,再成功发展到低于40nm级别的微型化。随着工艺和结构的深入发展,SoC面临的挑战越来越大(如集成复杂度高、晶圆成本高、开发时间长等)。SoC通常是客户定制的,或者是面向特定用途的产品,开发成本较高。基于封装技术的系统集成方法提供了一条替代芯片上的系统集成并进一步延续摩尔定律的有效途径。

图1-1 SoC功能集成示意图
2005版《国际半导体技术发展路线图》对系统级封装的定义:采用任意组合将多个具有不同功能的有源电子元器件与可选择性的无源元器件,以及诸如微机电系统(Micro-Electro-Mechanical System,MEMS)或光学元器件等其他元器件组装成可以提供多种功能的单个标准封装件,形成一个系统或子系统。
20世纪60年代末到70年代初,贝尔实验室和IBM首次提出了IC封装的3D集成概念,封装体堆叠(Package on Package,PoP)封装进入起步阶段。PoP指的是在一个独立封装体顶部堆叠另一个独立封装体。早期的PoP与引脚通孔互连技术密切相关,利用双列直插式封装(Dual Inline-pin Package,DIP)的直插式引脚插入基板通孔,实现电镀通孔(Plated Through Hole,PTH)插装,形成板上堆叠。
随着DIP和PTH互连在20世纪70年代应用的增多,PTH互连技术在IC封装堆叠中的应用越来越广泛,堆叠结构开始出现各种演变,如DIP堆叠于插座,如图1-2所示。将DIP元器件插入背驮式插座中,再将背驮式插座插到PCB上的标准插座中,在背驮式插座的下方,另一个DIP直接插入PCB或标准插座中。20世纪80年代,出现了表面贴装技术(Surface Mount Technology,SMT)。利用呈J形、海鸥形的四面扁平无引脚(Qual Flat Package,QFP)封装技术可以直接将上封装体的引脚通过回流焊接技术焊接在下封装体引脚的焊盘处,从而实现上下两个封装体的堆叠。J形PoP如图1-3所示。富士通公司也开发出了将不同外引脚通过焊料堆叠进行互连的新封装方式,如图1-4所示。目前常用的PoP结构大多数采用球栅阵列(Ball Grid Array,BGA)封装,并通过金属锡球实现上下PoP,在提供上下封装体物理结合的同时,实现电路互连。

图1-2 DIP堆叠于插座

图1-3 J形PoP

图1-4 通过焊料堆叠进行异表引脚封装示意图
这些早期IC封装的3D集成都是在基板Z轴方向封装体上的简单堆叠,只简单追求功能的扩展,并未专注于系统结构的微型化。
1971年,Alfred D. Scarbrough在US05/111476专利文件中首次提出了穿透晶圆实现互连的晶圆堆叠概念。带有存储芯片的晶圆与结合互连和空腔的晶圆都有穿透晶圆的通孔,通孔中填满导体,通过可延展的接触点连接两个晶圆上穿透晶圆的通孔,在一定压力和温度作用下键合,实现晶圆堆叠。
直至20世纪80年代,通用电气、IBM和伦斯勒理工学院才真正实现晶圆堆叠的关键性工艺,即硅通孔(Through Silicon Via,TSV)技术,在芯片与芯片之间、晶圆与晶圆之间通过垂直传导实现互连。早期的TSV采用硅的双面各向异性化学蚀刻方法制作。TSV技术可以实现芯片在Z轴方向最大限度的堆叠、在Z轴方向最短距离的电性连接,不仅可以提高芯片运行的速度,还可以最大限度地降低功耗,因此,越来越多的公司开始研究各种更先进的TSV制作工艺。TSV技术的出现,真正开启了封装微型化与系统集成兼容的先河。
20世纪80年代,IBM、Fujitsu、NEC与Hitachi先后发明了高度复杂的多芯片模块(Multi Chip Module,MCM)。MCM技术将多个测试良品(Known Good Die,KGD)IC贴装在多层衬底基板上进行水平2D互连,以实现系统功能的集成,如图1-5所示。早期的多层衬底基板采用高温共烧陶瓷(High Temperature Co-fired Ceramics,HTCC),即多层陶瓷,采用三氧化二铝金属化,并采用多层共烧钼或钨互连。随后,这些材料被低温共烧陶瓷(Low Temperature Co-fired Ceramics,LTCC)等高性能陶瓷取代,采用更小绝缘常数的陶瓷制造,如玻璃陶瓷,利用导电性更好的电导体铜、金、银、钯等进行金属化。第三代MCM技术进一步改进,添加了多层有机绝缘层和更小介电常数的导体,溅射或电镀了具有更好电性能的铜。
当前主流的芯片堆叠始于20世纪90年代,这些芯片堆叠互连方式包含侧面金属互连、引线键合(Wire Bonding,WB)、载带自动键合(Tape Automated Bonding,TAB)。1992年,欧文传感器公司发明了侧面金属互连技术:将相同结构的裸芯片表面焊盘进行金属重布线,将焊盘的导通路径重布线至芯片的端边,再将裸芯片直接堆叠,芯片侧边沉积金属形成侧面电互连焊盘。通过互连这些侧面焊盘实现堆叠裸芯片之间的垂直互连,开启了现代非TSV芯片堆叠封装的先河。这种金属化堆叠方法最初是用于堆叠相同尺寸硅芯片的,随后也被应用在不同尺寸的芯片上。

图1-5 MCM 2D互连示意图
大量基础工艺在芯片堆叠封装中的逐步开发和应用,推动引线键合工艺从20世纪90年代开始逐渐广泛应用于芯片堆叠。引线键合堆叠经常应用于同样尺寸的芯片或底部是较大芯片的金字塔结构或悬挂堆叠结构中。引线键合堆叠示意图如图1-6所示。而后,出现了引线键合工艺与倒装工艺结合的芯片堆叠封装,如图1-7所示。倒装芯片(Flip Chip,FC)可以根据产品设计目的设定为顶部芯片或底部芯片。

图1-6 引线键合堆叠示意图

图1-7 引线键合工艺与倒装工艺结合的芯片堆叠封装示意图
以上多芯片封装都是芯片与芯片的集成封装,或者子封装体与子封装体的集成封装,主要出发点都是扩展芯片的功能,还没有注重芯片与基板的系统集成。直到20世纪90年代中期,乔治亚理工学院封装研究中心提出了系统集成技术,将IC、封装体、无源元器件通过系统基板集成到一个单一的封装体,如图1-8所示,真正实现了系统级的集成和微型化。从此,系统级封装开始以有机基板为主要承载体,以MCM、PoP、多芯片堆叠封装、SMT无源元器件等不同形式进行系统集成。
进入21世纪,IC制造和应用开始迅猛发展,在基板单侧系统集成的基础上出现了基板双面系统级封装,如图1-9所示;在圆片级封装的基础上出现了圆片级系统级封装,如图1-10所示。一个包含多芯片、多模块的单一封装系统通过数字、射频、光学、MEMS的协同作用可以实现所有系统功能,从而可以满足物联网时代的多功能要求。

图1-8 系统级封装示意图

图1-9 基板双面系统级封装

图1-10 圆片级系统级封装
随着系统集成应用越来越广泛,微型化、功能集成度要求越来越高,21世纪初在多层基板基础上出现了埋入式基板,即在基板内层中埋入无源元器件、有源芯片,从分立式埋入到薄膜埋入,使基板功能化,基板表面的芯片或元器件贴装尽可能节省空间,整个系统封装尽可能做得更小。本质上,埋入式基板系统级封装是基板技术的革新,并且在3D Z轴方向实现了高效率的系统集成。
随着无线通信的迅猛发展,低时延、大容量、高速率网络需要承载人与人、人与物,以及物与物之间的相互交流。要实现这样的高速通信要求,必须解决一个核心技术问题,即如何使用大规模天线阵列降低毫米波移动信道的路径损耗。2006年,出现了天线封装(Antenna in Package,AiP)这一新颖的天线解决方案,将天线与芯片集成在封装体内。最初的AiP将天线集成在陶瓷基板上,由于局限性比较大,因此后来将目标转向有机PCB。将天线印制在顶层PCB上,信号线与封装体接地实现在底层PCB上,顶层PCB与底层PCB之间形成腔体以在其中设置电路芯片。这一方案不仅可以满足天线小型化需求,而且天线与芯片可以实现最大程度的靠近,减小路径损耗。AiP的技术特征属于系统级封装概念范畴。AiP技术的早期研究主要围绕2.4GHz蓝牙芯片展开,中期研究主要围绕60GHz芯片及毫米波雷达展开。随着5G的商用,对应AiP的研发则向大于或等于6GHz的主流频段扩展。另外,围绕物联网(Internet of Things,IoT)及毫米波通信5G芯片,人们也在开发将天线、射频前端和收发器整合成单一系统级封装体的方案。
除利用封装载体表面或内部的系统集成外,扇出型(Fan-Out,FO)封装不仅可以整合多芯片封装,而且性能更佳。2009年至2010年,扇出型晶圆片级封装(Fan-Out Wafer Level Package,FOWLP)开始商业化量产。但是,早期的扇出型圆片级封装只应用于单芯片,并未实现系统级封装。2014年,台积电开发了集成扇出型(Integrated Fan-Out,InFO)封装技术并成功应用,实现了该技术的商业化,在实现系统功能集成的同时降低了产品厚度,提高了芯片埋入灵活性,改善了电性能。所有扇出型封装虽然都可以用“芯片先装”“芯片后装”“芯片功能面朝上”“芯片功能面朝下”形式实现,但它们都是以芯片埋入塑封料为特征,采用导线引出的方式,通过介电层与重布线层,根据需要实现信号输出线路重新布置的。