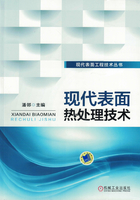
1.2.3 化学热处理后渗层的性能评估
不同的材料经各种化学热处理后,表面将获得不同厚度、成分、组织和性能的渗层,其目的是满足不同服役条件的需要,这也是选择化学热处理工艺方法、制订化学热处理工艺方案的依据。
1.硬度
经不同化学热处理工艺处理后所获得的渗层硬度是各不相同的。图1-16列出了几种化学热处理工艺的大致硬度范围。总的来讲,大部分化学热处理工艺都将使材料的表面硬度提高。
图1-15 渗碳温度及保温时间对渗层深度的影响
2.耐磨性
根据磨损条件不同,磨损可分为四大类,即磨粒磨损、黏着磨损、接触疲劳磨损和腐蚀磨损。这四种磨损的机理各不相同,破坏形式各异,因而对表面渗层也有不同的要求。
图1-16 几种化学热处理工艺的大致硬度范围
对工件表面所施加的应力不致使磨粒破碎这类低应力磨粒磨损,化学热处理具有较好的效果;在高应力磨粒磨损条件下,对材料的强度、韧性要求很高,而渗层一般较脆,因此,难以用化学热处理方法来提高这类工件的耐磨性。
材料抵抗黏着磨损的能力决定于材料的压缩屈服强度(或硬度)、韧性,凡能提高材料表面硬度、减小摩擦副之间两种金属结合力的化学热处理方法,都将显著提高材料的抗黏着磨损能力。
材料接触疲劳强度除与材料的冶金质量、工件表面粗糙度等因素有关外,采用适当的化学热处理可显著提高接触疲劳强度,即提高材料抗接触疲劳磨损的能力。
典型的腐蚀磨损有氧化磨损、气蚀、微动磨损及特殊介质磨损等。致密而非脆性的氧化膜能显著提高磨损抗力。渗碳(碳氮共渗)、氧氮共渗、渗氮(氮碳共渗)等处理,可提高工件抗腐蚀磨损的能力。
3.减小摩擦及抗擦伤性能
渗氮、氮碳共渗、渗硫等化学热处理方法,可降低材料表面的摩擦因数,起到固体润滑的作用,或是提高材料的抗咬合性能,防止工件表面擦伤。这些工艺广泛用于模具、滚动轴承、工具、轴类等零件的表面处理。
4.弯曲疲劳强度
渗碳(碳氮共渗)、渗氮(氮碳共渗)等化学热处理工艺,能使工件表面产生残余压应力,可提高材料的弯曲疲劳性能。
5.抗氧化性和耐蚀性
锌、铝、铬、硅等元素的渗入,或者是在工件表面形成致密的保护膜,或者是提高基体的电极电位,都有利于提高工件的抗高温氧化性和耐蚀性,这也是化学热处理的一个重要任务。